DX InitiativesProductionmanagement and traceability using DX
In-house construction and operation of DX systems
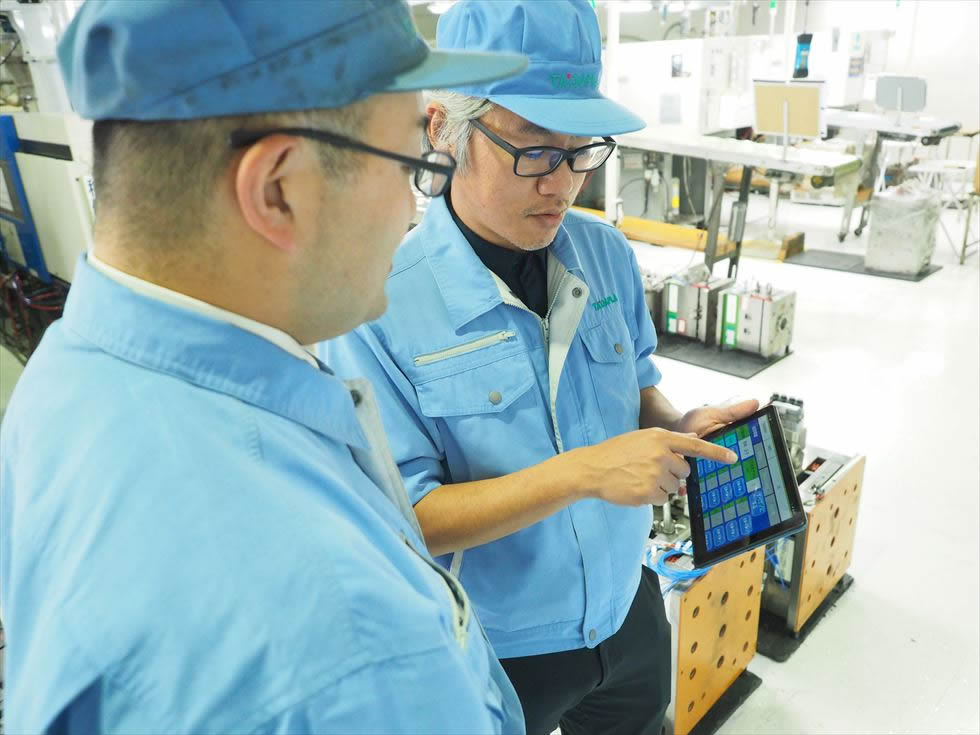
Tadapla utilizes digital transformation for traceability and production management.
Real-time management is achieved by placing tablets at the site and inputting daily production status and results.
By centrally managing all production data within the company, such as when, with which material, and on which molding machine it was produced, we can take immediate Applicable in the unlikely event that a defect occurs, immediately identify the affected lot, and quickly deliver replacement products, thereby minimizing market complaints.
We have a dedicated DX team in-house that works in cooperation with production sites to build and operate a practical, original Tadapla system.
#Visualization of production status
#IoT
#Traceability
#MES(Manufacturing Execution System)
#IoT management of processes
#Paperless
#Immediate Applicable when defective products are released
#DX
Production management/molding results (tablet and cloud management)
Inspection automation
In-mold pressure sensor
By quantifying the pressure inside the mold during the molding process and monitoring the pressure waveform in real time, we can distinguish between good and defective products.
If a product is determined to be defective, it is automatically taken out of the line, preventing defective products from being mixed into mass-produced products.

Production management/molding results (tablet and management system)
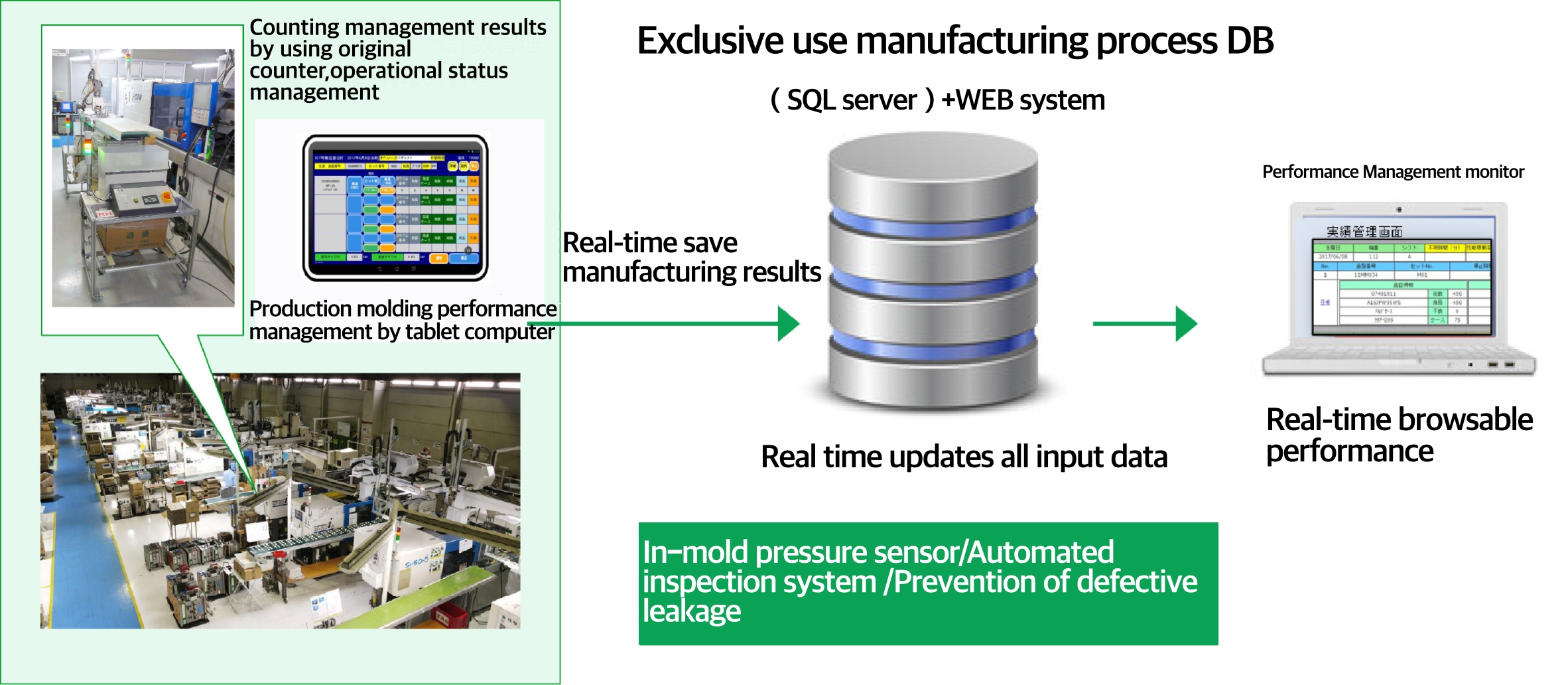
Daily production report (visualization)
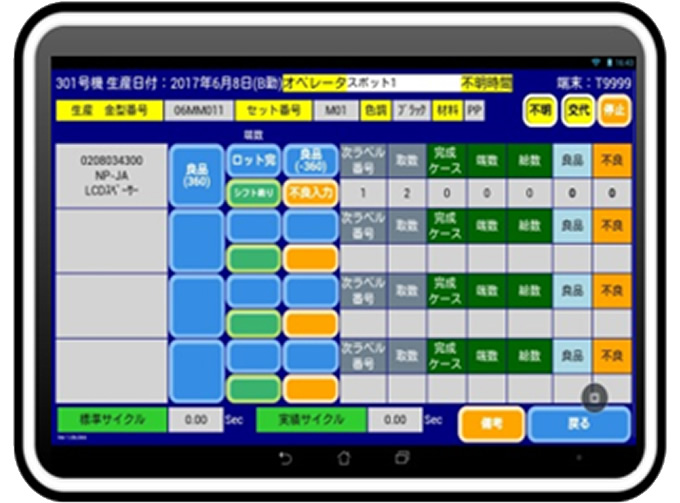
We have achieved centralized data management by placing tablets at the site and inputting daily production status and results.