Foam molding bypolyurethane
Environmentally friendly, non-freon insulating foam (cyclopentane foam)
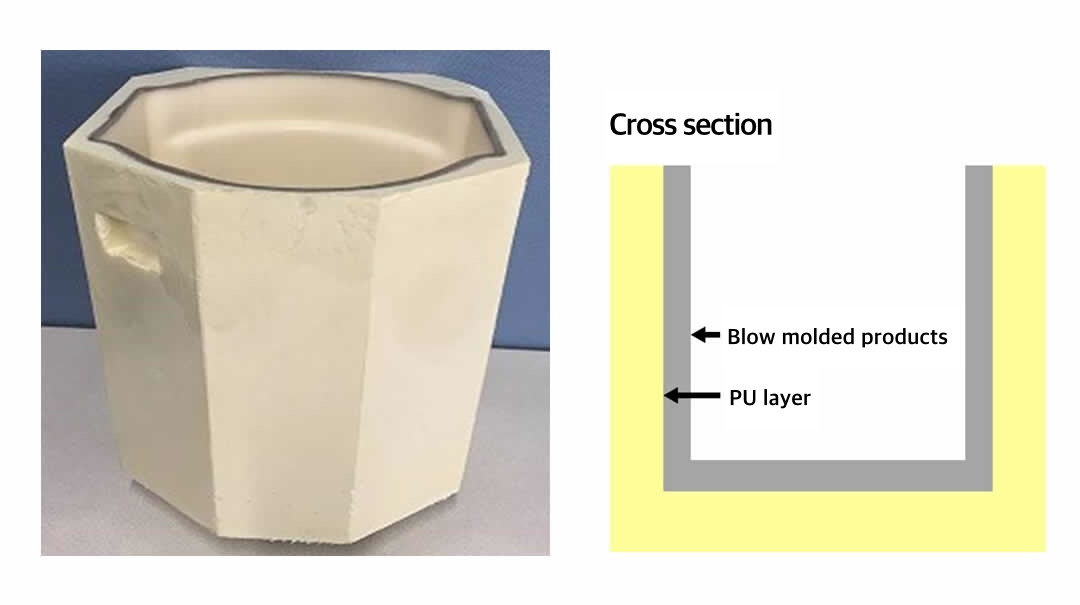
Rigid polyurethane insulation, which has higher insulation performance/insulation technology, is now widely used.
In order to promote environmental friendliness, our company was one of the first in Japan to introduce cyclopentane foaming equipment (which uses a material with zero ozone depletion potential and extremely low global warming potential) in 1994.
Polyurethane foam has a history of about 40 years, and over those years we have improved our insulation performance and insulation technology. Using high-pressure foaming methods such as PU Form Mold Automation and multi platen press foaming, we have achieved an initial thermal conductivity of 0.021 W/mk in terms of performance, and we also set the core density to match the performance required by our customers.
Tadapla 's SDGs Initiatives
Tadapla is working towards the SDGs as a manufacturing company using environmentally friendly molding technology.
The hard urethane we use is made from high-performance urethane (cyclopentane material) that has excellent insulating and environmental properties, and is a non-fluorocarbon formulation.
In addition, it has an ozone depletion potential of 0, making its global warming potential extremely low.
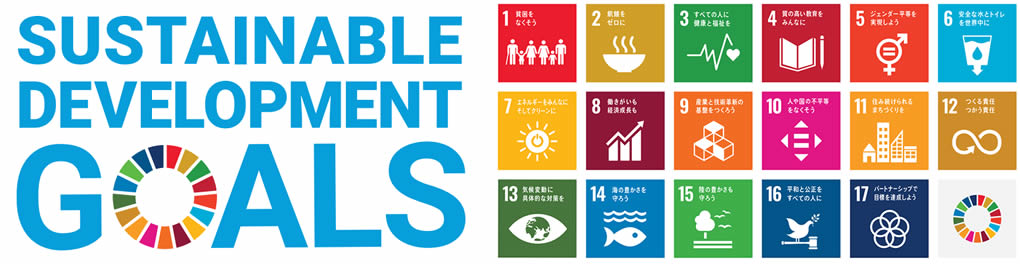
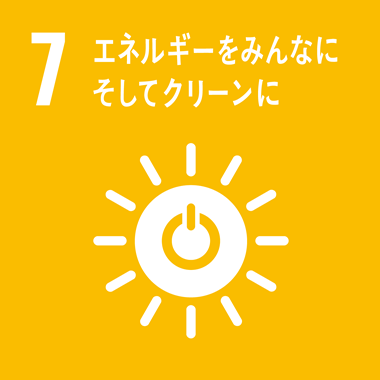
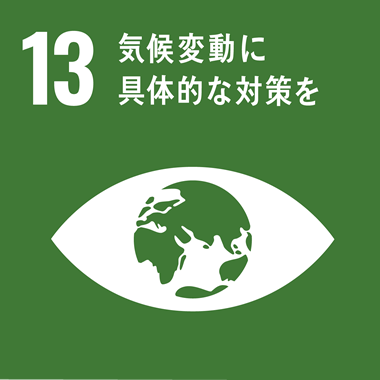
Polyurethane foam foam molding technology tailored to the product and shape
We have the technology and equipment Polyurethane foam molding, including PU Form Mold Automation, multi platen press foam, and Box Shape by PU Foam Mold Manual.
Taking advantage of urethane's characteristics such as light weight and heat insulation, we propose a variety of uses for the material, including applications in home appliances and daily necessities.
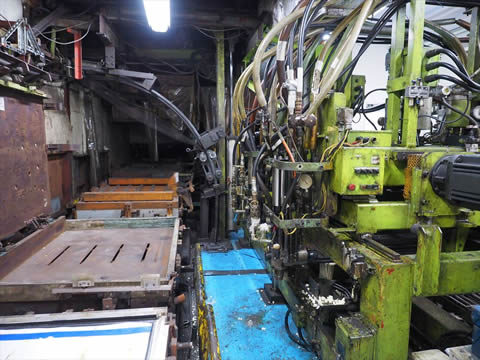
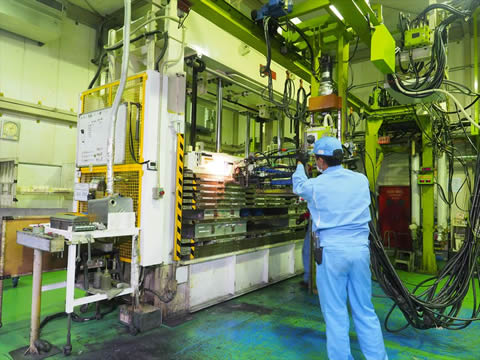
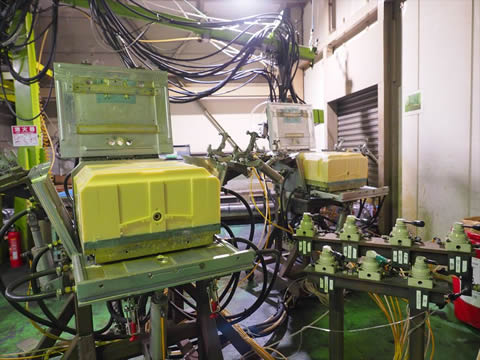
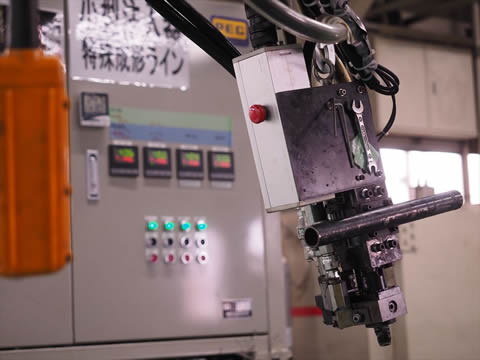
We propose products that utilize the characteristics of urethane and suggest shapes and molding methods to suit the purpose and environment of use. We also focus on developing molding techniques to prevent warping and deformation, by creating an in-house development environment to meet customer needs. In addition, the technology to manufacture curved, deformed floor covers is unique to TADAPLA.

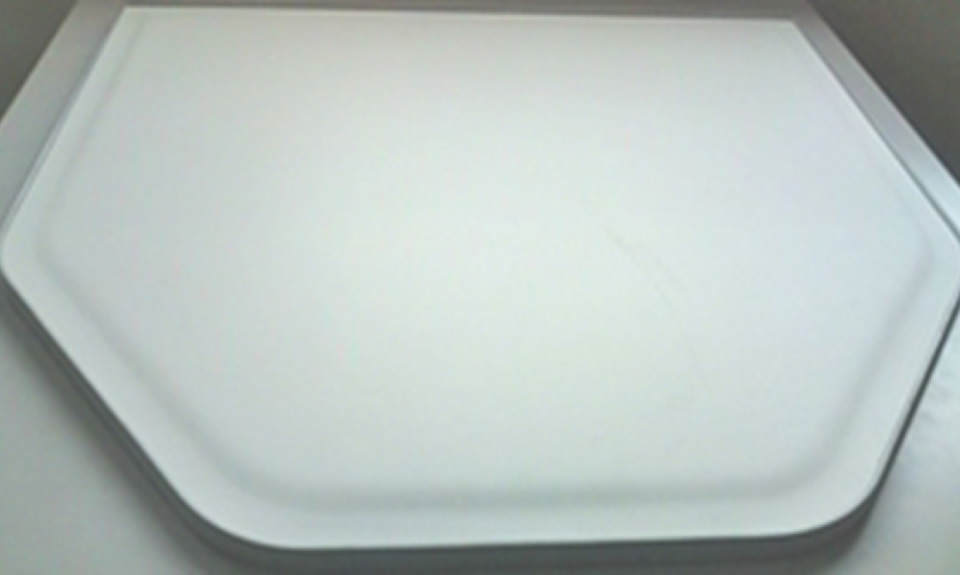
Product track record
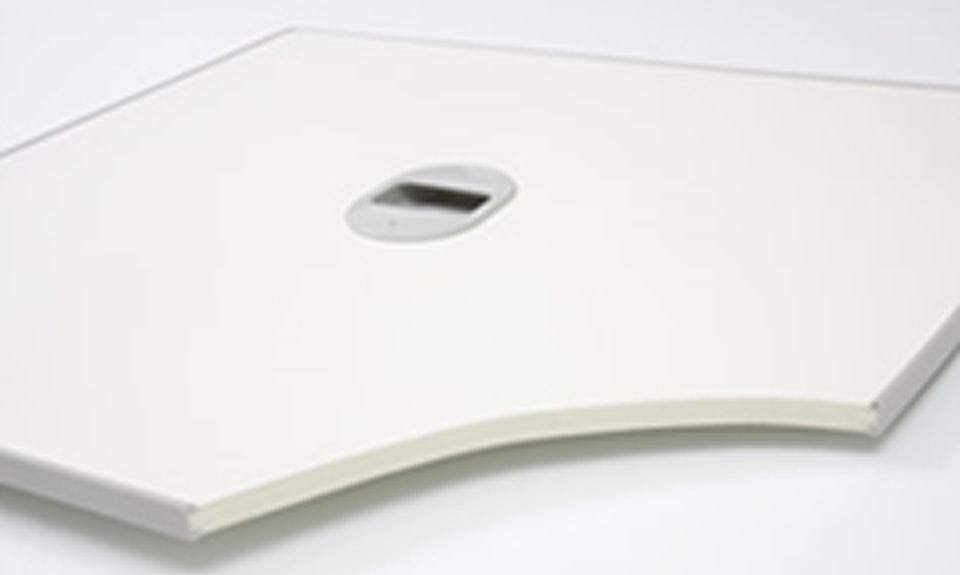
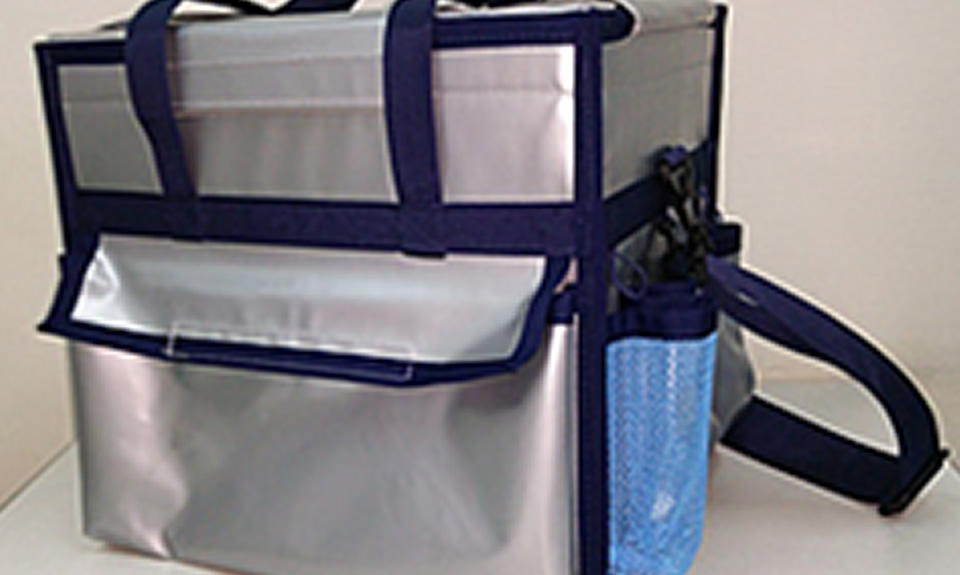
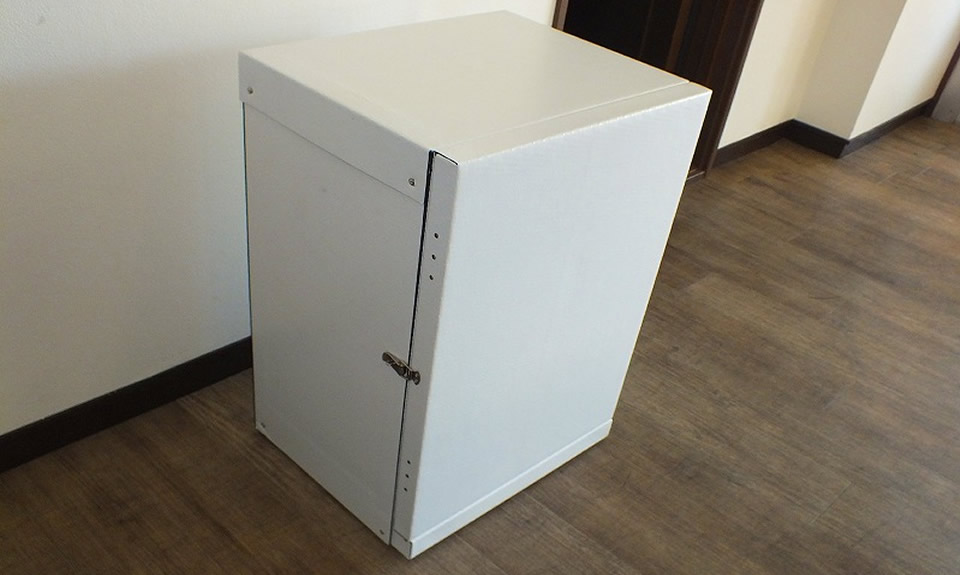
Molding Size
Unit (mm) | vertical | beside | High |
---|---|---|---|
PU Form Mold Automation | 1540 | 1030 | 100 |
1500 | 1030 | 200 | |
Plate Shape by PU Foam Mold Manual (multi platen press) | 1300 | 3000 | 80 |
1300 | 3000 | 140 | |
1300 | 3000 | 170 | |
Box Shape by PU Foam Mold Manual (For small-scale production and prototype testing) |
Please contact us for size |
* The dimensions that each equipment can produce vary depending on the shape. Please contact us for details.
In-house developed products
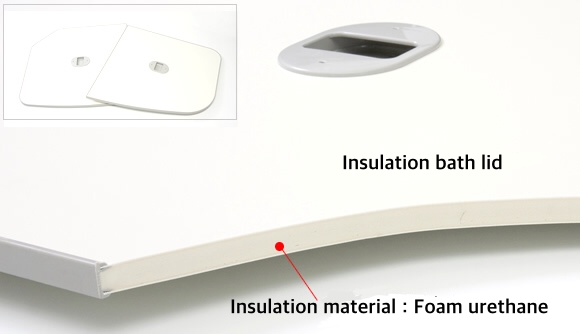
In-house developed insulating floor covering Using urethane that is environmentally friendly, lightweight and insulating (thermal conductivity 0.021 w/mk), and combining technology cultivated over many years, and a strong passion to "use Polyurethane foam to create the floor covering that customers want!", an insulating floor covering that combines "high insulation and high rigidity" was born.
We have also set up an insulation floor laboratory, and have received factory registration and Model Number certification from the Product Safety Association (SG Mark).
Currently, we have succeeded in developing a "transformable heat insulating floor cover" that fits the curved shape of bathtubs, and are actively Applicable to customer needs. In order to further improve, we are also working on research and development with the aim of "reducing the weight of bath covers" while maintaining the current performance.